Chemical Recycling Europe (CRE) rejects claims made in Zero Waste Europe report on pyrolysis
Position Paper
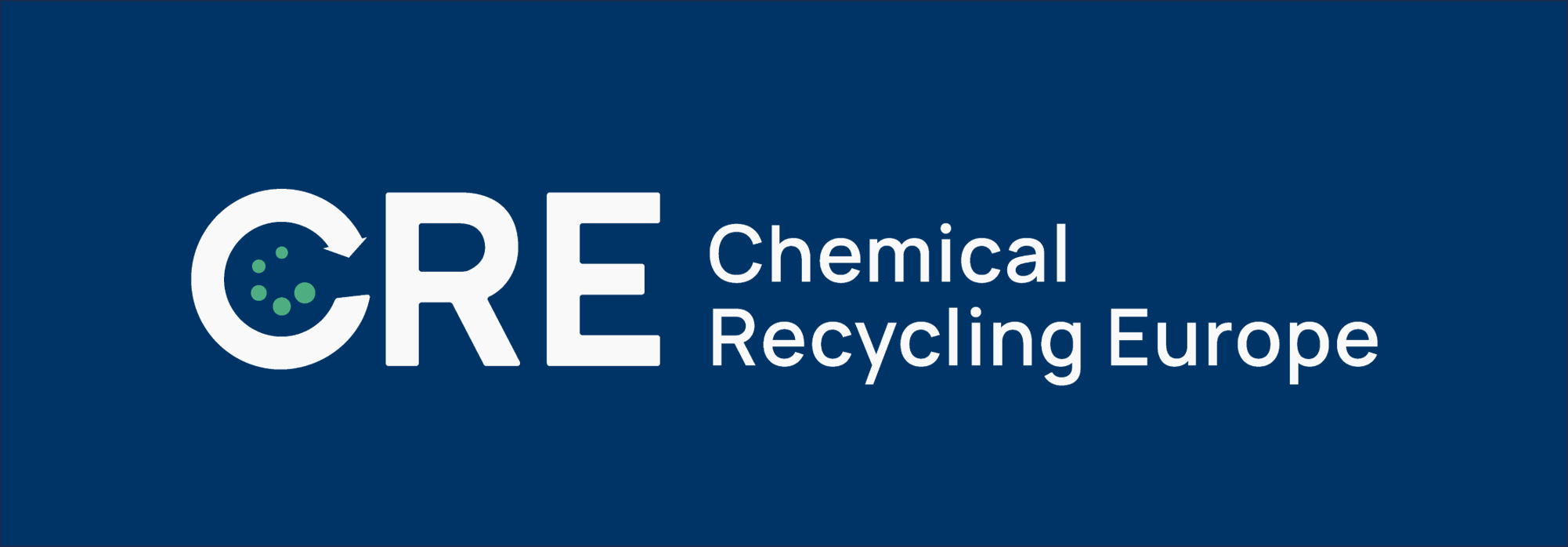
Chemical Recycling Europe, the association representing technology providers in chemical recycling, is sounding the alarm on the grave misinterpretation of facts and scientific evidence on pyrolysis laid out in Zero Waste Europe’s recent report Leaky loop ‘recycling’ published on 26 October.
Pyrolysis is one of the main chemical recycling processes in Europe and globally. Investment and capacities are growing steadily with pyrolysis being the most commercially advanced with an expected total installed capacity of 1.7 million tonnes in 2028 in Europe1. This capacity focuses on processing mixed plastic waste that cannot be mechanically recycled. Outputs from pyrolysis capacity will be used to produce food grade recycled content, essential for fulfilling the mandatory plastics recycled content targets as well as to increase recycling rates. Currently, in Europe, there is no other authorised recycling process that can produce food grade recycled content for polyolefins at scale.
The European Commission’s Joint Research Centre has defined chemical recycling technologies including pyrolysis as currently undergoing rapid technological advances2. Several pyrolysis processes as well as other chemical recycling technologies have been analysed by the JRC as well as by other independent scientific bodies. There is a wealth of research and data that could have been used to draw conclusions on the status quo of pyrolysis, however, the report focuses on drawing conclusions based on a narrow set of inconclusive evidence to obscure facts.
Contrary to what is claimed in the report, chemical recycling technologies do not exist to replace the need for reduction in plastic waste generation and plastic reuse, both being part of the EU waste hierarchy together with recycling3. CRE wholeheartedly embrace the waste hierarchy, where reduction and reuse are crucial and central. These measures are needed alongside recycling via different technologies, including pyrolysis, to tackle plastic waste pollution. The challenge of achieving plastic circularity requires multiple sustainable solutions working together.
Pyrolysis as a process has many and varied applications and can process different waste streams. Different waste streams have diverse waste input specifications and levels of contamination, resulting in different pyrolysis oil specifications and characteristics. Most conclusions in the report do not contextualise the fact that there is a wide range of pyrolysis process configurations and plant arrangements with each of these producing different pyrolysis oil grades that, in turn, have different downstream processing characteristics.
The incentives for pyrolysis technologies are manifold and increasingly clear. This includes the need for technologies that can process currently unrecyclable plastic waste streams. The business case has grown stronger in line with technological advancements, better segregated plastic waste feedstocks, and less contamination as collection and sorting evolved over time. These incentives and the need for scaling is true for other recycling technologies as well, including mechanical recycling.
In the past, incineration with energy recovery was favoured as circular solutions for materials were rarely considered or incentivised, and this contributed to making pyrolysis less attractive to the market. However, as the need for circular solutions is now prioritised, the market has shifted, clearly evidenced by the investments into chemical recycling of which pyrolysis is the largest and most commercially established. The environmental benefit of incineration with energy recovery has severely diminished over time and chemical recycling through pyrolysis is able to recycle plastic waste with a significantly lower environmental impact while also keeping material into circulation, something that incineration cannot do. Policy drivers and the need for reducing landfill and incineration have also significantly contributed to an imperative for more recycling technologies. We expect that favourable market conditions for the uptake of pyrolysis to continue to grow in the future.
The report further mentions several policy and technical issues using misleading arguments. We discuss some of these below.
There are well-established rules on how to classify waste to products, which must be fulfilled under the Waste Framework Directive, national legislation on end-of-waste criteria as well as through REACH product registration. End-of-waste legislation for pyrolysis outputs is currently established through member state criteria defined at national level and we encourage harmonisation of these criteria at European level.
At current production levels of pyrolysis oil compared to the installed ethylene capacity in Europe which is 25.305 kta, dilution is the only feasible option to offtake pyrolysis oil for polymer production4. This is well known and accepted by all stakeholders since the goal of the industry is to scale these quantities to gradually replace naphtha using the existing petrochemical infrastructure. Installing separate infrastructure to process pyrolysis oil for polymer production would incur a high economic and environmental cost.
This also ensures purification is not needed at current levels. However, as the goal is to increase the volumes of pyrolysis oil, purification and upgrading will be needed to ensure alignment between pyrolysis oil specifications and the ones of steam crackers and refineries. Some industry players have installed or are planning to install purification and upgrading capacity as part of their collaboration with pyrolysis technology providers and petrochemical partners. This is not a new development, nor does it affect the circularity benefits of pyrolysis oil.
Additionally, virgin naphtha, which pyrolysis oil is a replacement for, often requires steps of purification to meet specifications. Virgin naphtha is a by-product of the diesel-hydrotreater in refinery processing. This process “purifies” the distillates from previous conversion and separation processes to fulfill the requirements and specification of downstream processing. In such processes, the contaminants naturally present in virgin oil at first and in distillates afterwards are removed. Furthermore, naphtha differs depending on what virgin oil is produced from and the production facility. Virgin naphtha is not a homogeneous product, this in turn leads to different needs in terms of the purification steps.
The author's reference to "contaminant limits" in steam crackers lacks specificity regarding the nature of these limits, the specific steam crackers to which they apply, and the sources from which this information is derived. It is important to note that steam crackers exhibit considerable variability in their specifications, making blanket statements unsuitable for characterizing them comprehensively. Moreover, several statements pertaining to pyrolysis oils are overly generalized and may not account for variations in feedstock sources. For instance, some references to wood and cellulose as contaminants may be contextually accurate for certain pyrolysis processes, such as those dealing with wood-based feedstocks. However, these references may not hold true when addressing plastic waste streams, where wood and cellulose contamination is often negligible.
Failing to provide the necessary context for these statements in relation to a specific plastic waste stream can be highly misleading. It is crucial to recognize that the majority of pyrolysis capacity, whether currently operational or planned, primarily targets mixed post-consumer or post-industrial plastic waste as its designated feedstock input. This distinction is significant because it underscores the fact that different waste streams, such as auto shredder residue (ASR) and waste electrical and electronic equipment (WEEE), may indeed necessitate distinct preparatory steps before undergoing pyrolysis and subsequent upgrading processes.
It is well-established that purification and upgrading processes are routinely applied to fossil virgin oil, and transitioning to pyrolysis oils as a new feedstock entails relatively minor adjustments. These refinements can be likened to the ongoing adaptations made in traditional refineries when switching between different fossil oil sources. Therefore, it is essential to emphasize that pyrolysis processes are versatile and can be tailored to the specific characteristics of the input feedstock, ensuring effective conversion and quality outcomes.
Post-consumer plastic waste is a heterogeneous mixture comprising various plastic types intermingled with contaminants. This inherent diversity poses substantial technical and economic challenges when considering mechanical recycling processes. While it is feasible to mechanically recycle certain post-consumer flexible plastic waste to some extent, it is crucial to recognize that a significant portion of flexible and multi-layer flexible packaging materials presents insurmountable obstacles for mechanical recycling due to their complex composition and intricate layering. The resultant outputs are often constrained in terms of quantity and value, compounded by polymer degradation with each successive recycling cycle. Furthermore, these outputs typically fail to meet the stringent standards required for food-grade applications.
This is precisely where the value proposition of pyrolysis emerges as an attractive alternative. Pyrolysis processes offer a means to effectively address the challenges posed by the diverse and contaminated nature of post-consumer plastic waste. It enables the conversion of such challenging materials into valuable products.
Furthermore, life cycle assessment (LCA) studies play a pivotal role in comprehensively evaluating the environmental footprint of recycled plastics. These studies consider various aspects, including the impact of hydrotreatment upgrading after pyrolysis. The insights drawn from these assessments are rooted in empirical data obtained from technology providers, aligning with the body of scientific research within this field5.
Chlorine is not a major issue for the steam cracker itself but for the downstream processes and equipment such as the heat-exchanger. This is because chlorine is condensed with water to form hydrochloric acid, which is corrosive, or combines with nitrogen to form ammonium chloride and this can affect the performance of the heat exchanger. If chlorine content must be reduced to the current specification of fossil steam cracking naphtha, the reduction of three order of magnitude, as stated in the document, would be from maximum 1000 mg/kg to 10 mg/kg, which is generally accepted as the desired chlorine specification. Chlorine purification requires minimal amounts of hydrogen, if hydrotreatment is the preferred procedure. Other technologies at pilot and demonstration scale would not even require hydrogen treatment. Whether purification is necessary or not is a question that is highly dependent on the specific waste stream that is used as input feedstock as well as the specific pyrolysis process. PVC, for example, which can impact chlorine levels in pyrolysis oil is present in very minimal quantities in collected post-consumer packaging waste and this is not a problem for many of the pyrolysis operators who target this plastic waste feedstock. In some cases, an additional sorting step before waste is fed into the pyrolysis process ensures alignment with the target waste feedstock specification.
Bromine can be present only in specific waste streams such as waste electrical and electronic equipment (WEEE) which are collected separately from other plastic waste streams such as post-consumer household plastics.
Metals are present in fossil virgin oil and by order of magnitudes higher than in pyrolysis oil. De-metallization processes are very well established in petrochemical processes.
‘Free radicals’ are present in steam cracking and lead to the formation of the targeted outputs. This is similar to pyrolysis.
PAHs are formed during pyrolysis and this is similar to the production of PAHs during steam cracking of fossil naphtha. If present in pyrolysis, PAHs will be separated from monomers during steam cracking to fulfill the current specification of monomers. PAHs are not found in products used for skin contact.
The formation mechanism of PCDD/Fs under pyrolysis conditions is controversial in the scientific community. It is false that pyrolysis itself produces PCDD/Fs without any additional external factor such as molecular oxygen from air and metallic catalysts as copper. However, strict monitoring programmes are in place under EU legislation.
In summary, Chemical Recycling Europe strongly refutes Zero Waste Europe's recent report on pyrolysis, citing a skewed interpretation of facts. Pyrolysis, a vital chemical recycling process, is steadily advancing globally to complement current recycling efforts. The report's selective use of inconclusive evidence disregards extensive research and data on pyrolysis.
Efforts are underway to harmonise end-of-waste legislation for all recycling technologies including pyrolysis. Dilution remains practical at current production levels, with purification becoming necessary as volumes increase, this being well accepted across the industry for many years now. The report's concerns about contaminants lack contextualization, overlooking variations in waste streams and pyrolysis processes. Chemical Recycling Europe urges stakeholders to consider the nuanced understanding of pyrolysis, emphasizing its integral role in a holistic approach to plastic circularity. The evolving landscape of recycling technologies and market dynamics should be considered for a more informed perspective.
Position Paper ends
CRE ZWE rebuttal_position paper.pdf
PDF 123 KB
1 Available at https://www.plasticstoday.com/advanced-recycling/icis-now-tracks-pyrolysis-oil-pricing-chemical-recycling
2 Joint Research Centre 2023, Environmental and economic assessment of plastic waste recycling, available https://publications.jrc.ec.europa.eu/repository/handle/JRC132067
3 EU waste hierarchy and the Waste Framework Directive, available at https://environment.ec.europa.eu/topics/waste-and-recycling/waste-framework-directive_en
4 Available at https://www.petrochemistry.eu/about-petrochemistry/petrochemicals-facts-and-figures/cracker-capacity/
5 Consumer Goods Forum, Life cycle assessment of chemical recycling for food grade film, available at https://www.theconsumergoodsforum.com/wp-content/uploads/2022/04/Life-Cycle-Assessment-of-Chemical-Recycling-for-Food-Grade-Film.pdf